Our Capabilities
We work on the cusp of innovation and technology to deliver quality parts to our customers around the world. From startups to Fortune 500 companies, Gretna works with some of the world’s most respected companies. Using the latest industry tools and equipment to meet and exceed required tolerances, we provide 100 percent quality assurance.
Equipment
CNC Lathes
Distance Between Centers 20.0″ – 123.8″
Max. Turning Length 16.5″ – 120.0″
Max. Turning Dia. 15.7″ – 35.4″
Spindle Bore Dia. 2.1″ – 12.6″
Manual Engine Lathe
Distance Between Centers Up to 120″
Table Size 10″ – 22″
Spindle Bore 2″ – 3.5″
CNC Mills
X 30.0″ – 60.63″
Y 16.0″ – 29.92″
Z 20.0″ – 29.92″
A Full 4th Axis
Full 5th Axis Capabilities, including vertical lathe
- High Speed Machining up to 15,000 rpm
Manual Milling Machines
X 15″ – 16″
Y 10″ – 14″
Z 42″ – 50″
NOTE: All manual machines are equipped with electronic digital read out, and power supply
For a complete equipment list, contact us today.
Material Alloys
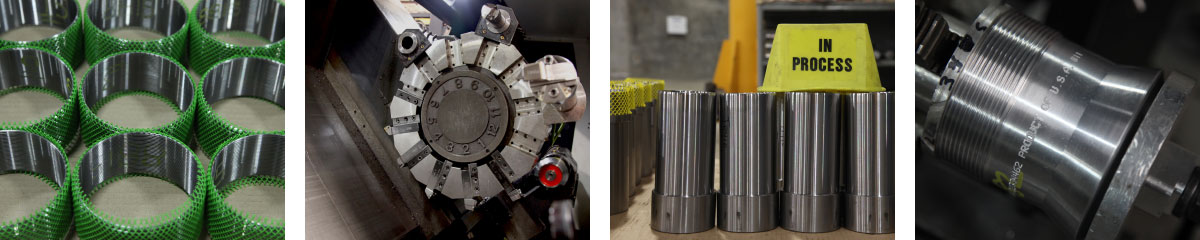
- Carbon and alloy steel (4130, 4140 thru 4145, 4340, 1018 thru 1026, 8620)
- Casing
- Cast iron
- Aluminum alloy (2011, 2024, 6061, 7075)
- Bronze and copper alloys
- Stainless steel (13-8, 17-4, 300 series, 410)
- 420 Modified, 13% Chromium, 9% Chromium, “Super” 13% Chrome
- Nickel alloys (Inconel – 925, 718, 625, K-50 Monel)
- Inconel
- Titanium alloys
- Monel
Programming
At Gretna, our CNC programmers are Class A machinists. This ensures that every drawing given by the customer is meticulously programmed by a person who has experience as a machinist. Furthermore, they also have the role of shop supervisors, which means that they are available to support the machine operators who may have questions during the setup or machining process. This cross training allows work to flow seamlessly from the customers’ print to the production floor.
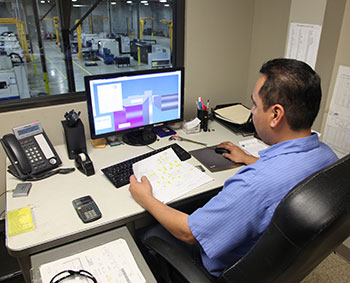
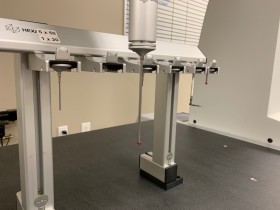
Inspection
Eliminating waste in the planning phase of a production process has an obviously beneficial impact on long-term profitability. Gretna’s inspectors have a combined 40 years’ experience of ensuring maximum efficiency, low cost and less waste, and they utilize state-of-the-art equipment, including a CMM, in a climate-controlled inspection room while adhering to a strict calibration schedule for quality assurance and control. Our inspection team gives top priority to ensuring quality is built into the production process by preventing or removing waste and recall issues.